JLR is advancing its journey toward sustainability by launching a £100 million circularity initiative aimed at cutting waste across its UK and European industrial operations.
This major effort focuses on reusing, refurbishing, repurposing, and recycling thousands of tools and pieces of equipment as the company prepares for the next phase of its electrification strategy, including the anticipated debut of the Range Rover Electric.
READ MORE: Ferrari 12Cilindri and 12Cilindri Spider Win Prestigious iF Design Gold Award
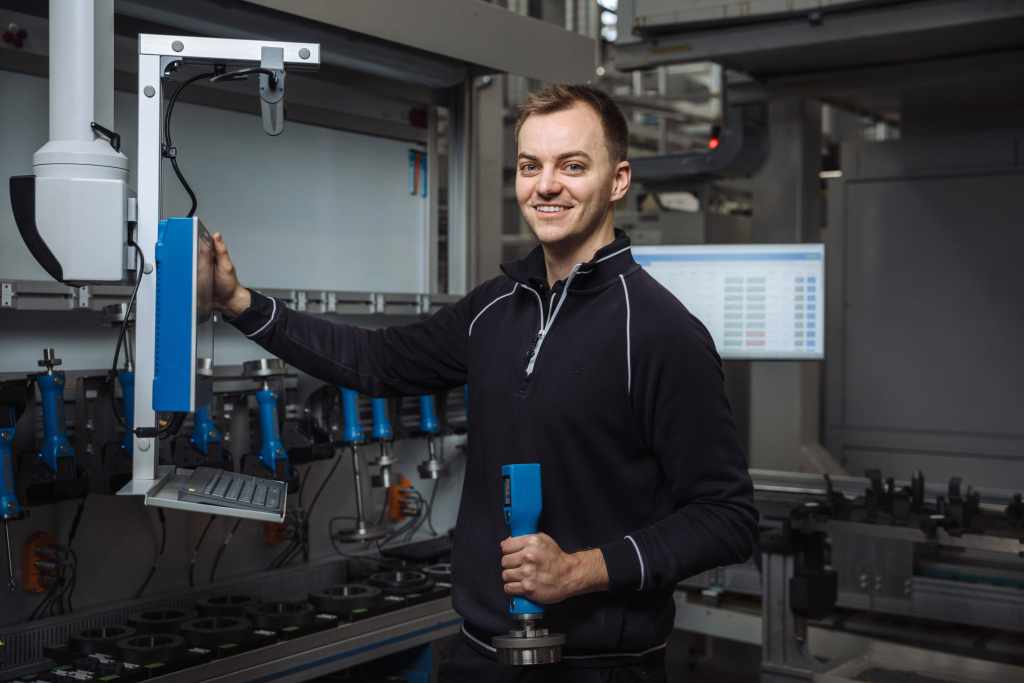
As part of this transformation, equipment from sites like Castle Bromwich, the Electric Propulsion Manufacturing Centre (EPMC) in Wolverhampton, and Graz, Austria has been assessed for reusability based on compliance, spare parts availability, refurbishment costs, and potential scrap value.
So far, more than 50,000 square meters of equipment—about the size of seven football fields—has been redeployed to JLR facilities in the UK and Slovakia instead of purchasing new.
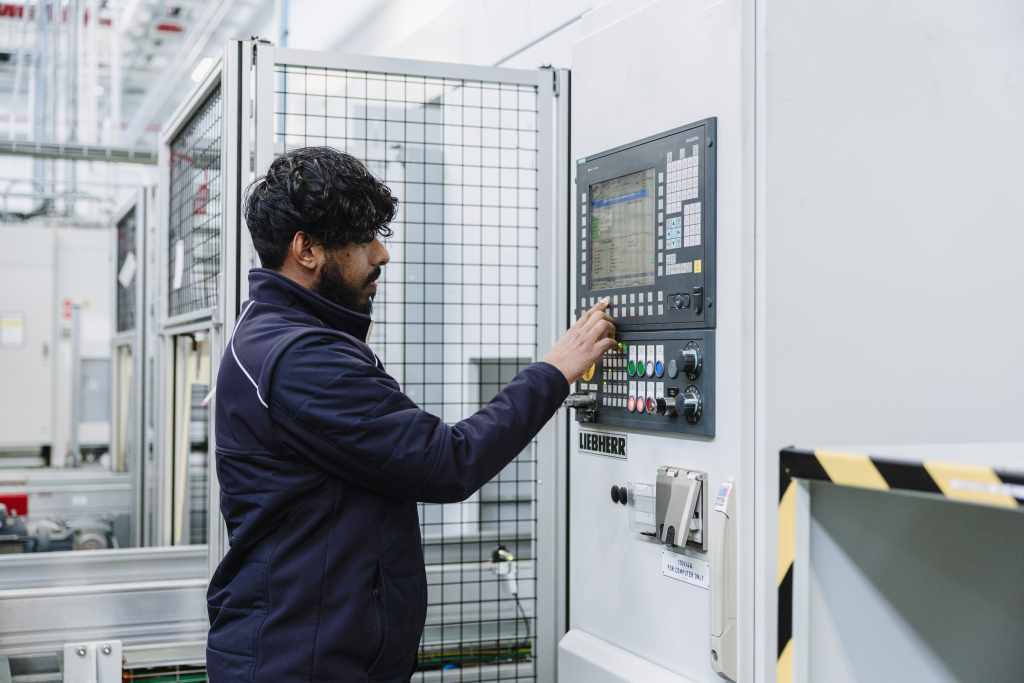
This includes hundreds of second-life robots now operational in Solihull, Halewood, and the EPMC, ready to produce next-gen EVs and battery packs. At the same time, 18,600 tonnes of scrapped metal have been recycled, avoiding the environmental impact of creating new steel from raw materials. By using recycled scrap instead of new steel, JLR helped cut CO₂e emissions by 1,258 kg per tonne, based on supplier data.
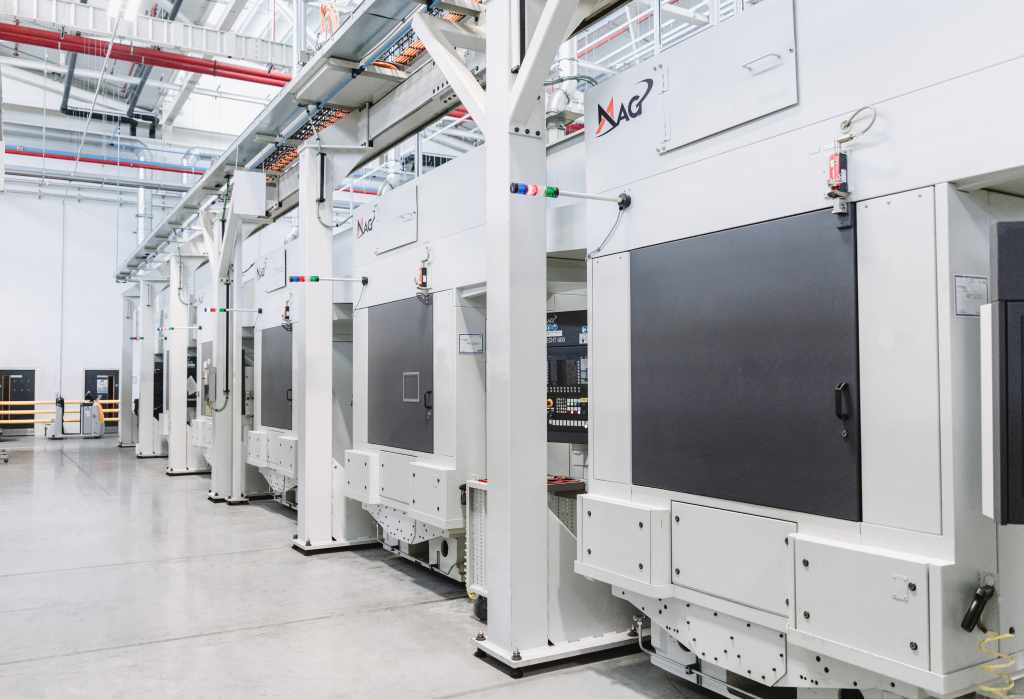
Andrea Debbane, JLR’s Chief Sustainability Officer, emphasized that this initiative not only helps the planet but also enhances profitability, supply chain resilience, and workforce development. “It’s not only the right thing to do,” she said, “but it also demonstrates that sustainable choices can reduce costs and unlock growth opportunities.”
The circularity effort is driven by a cross-functional team from Industrial Operations to Vehicle Programmes, and it includes the launch of a new in-house digital asset management system.
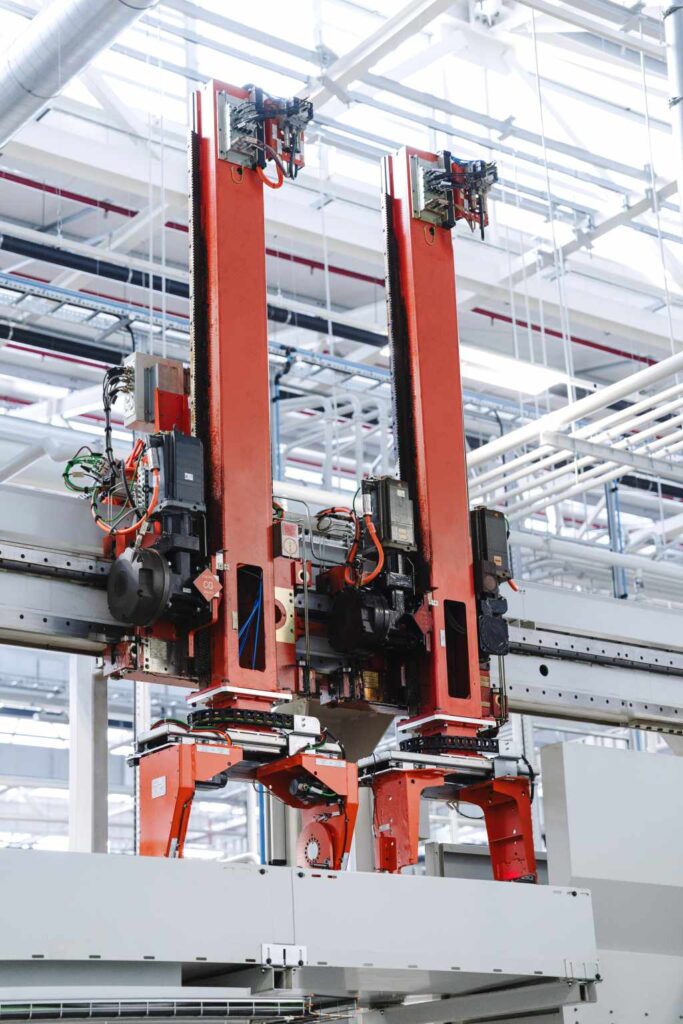
This system will track every asset’s lifecycle—from purchase to repurposing—and feature an internal marketplace to scale asset reuse across future projects. Additionally, teams have developed new skills in tool refurbishment, recalibration, and on-site safety, ensuring reused tools meet production standards.
This initiative plays a central role in JLR’s evolution into a modern, sustainable luxury brand. By addressing environmental impacts beyond tailpipe emissions and building circularity into its operations, JLR is aiming to set a new industry benchmark for environmental and social responsibility.
READ MORE: Retro Rides: Exploring the 1966 GM Electrovan, the World’s First Fuel-Cell Vehicle
Subscribe today for the freshest car news delivered to your inbox