BMW Group Plant Regensburg has introduced a cutting-edge autonomous transport vehicle to enhance the efficiency and safety of its press plant operations.
This driverless platform truck, powered by an electric drivetrain, can autonomously transport press tools and steel blanks with a payload capacity of up to 55 tonnes, navigating through the plant at a speed of four kilometers per hour.
This innovative logistics solution, unique in the world, relies on advanced LiDAR (Light Detection And Ranging) sensors, a key 3D technology for autonomous driving and automated processes.
READ MORE: The New MINI Countryman D Favoured Trim: Efficiency Meets Signature Driving Pleasure
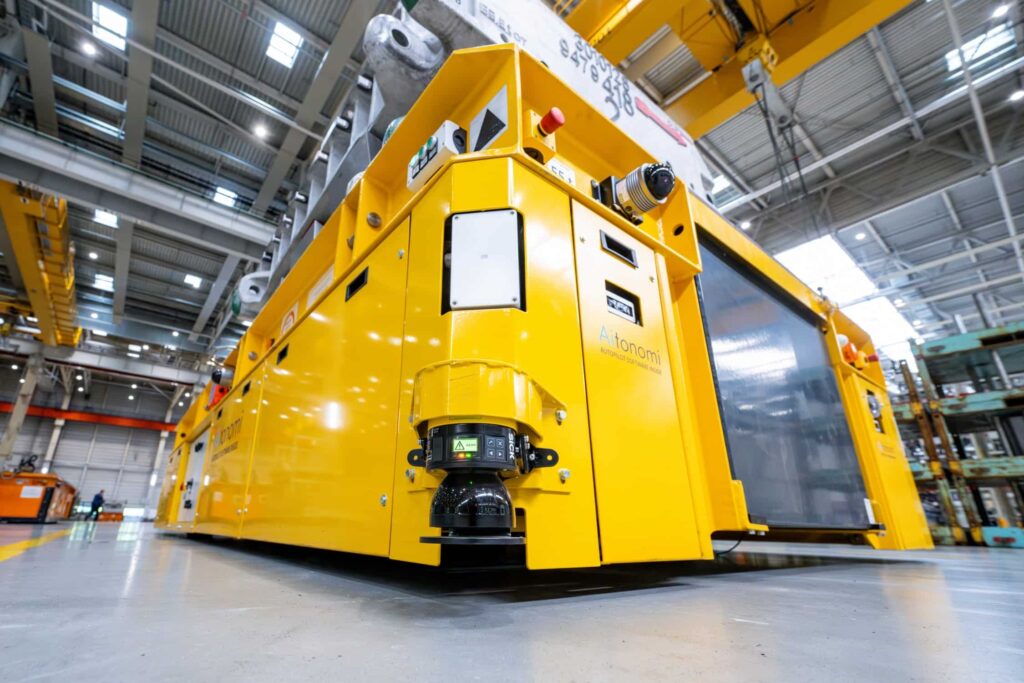
Tobias Müller, press plant maintenance manager at BMW Group Plant Regensburg, highlights the significant benefits of this emission-free electric vehicle. “The rollout of autonomous logistics solutions holds tremendous potential.
It will enhance manufacturing efficiency, flexibility, reduce transport journeys, and lead times. This not only boosts productivity but also saves energy and improves occupational safety for our employees,” he stated.
Use of Innovative LiDAR Sensor Technology
The new autonomous transport vehicle utilizes state-of-the-art LiDAR technology from manufacturer Pefra. LiDAR sensors are critical for autonomous driving and automated processes, providing accurate navigation, obstacle detection, and distance measurement.
These sensors, along with cameras and radar, create a 3D image (“scatter plot”) of the environment, ensuring safety and efficiency in complex settings like the Regensburg press plant.
BMW Group Plant Regensburg Operations
The press plant at Regensburg processes around 1,100 tonnes of steel daily, producing approximately 131,000 pressed parts each workday. It manufactures 113 different body components, including structural, reinforcement parts, and large outer panels like side frames, door skins, and bonnets from sheet steel up to 4.5 meters in length.
The plant’s most powerful press line uses high-speed servo technology, achieving a press force of 9,000 tonnes and a rate of up to 23 strokes per minute, making it one of the world’s fastest presses. These components are then assembled into vehicle bodies at the nearby body shop.
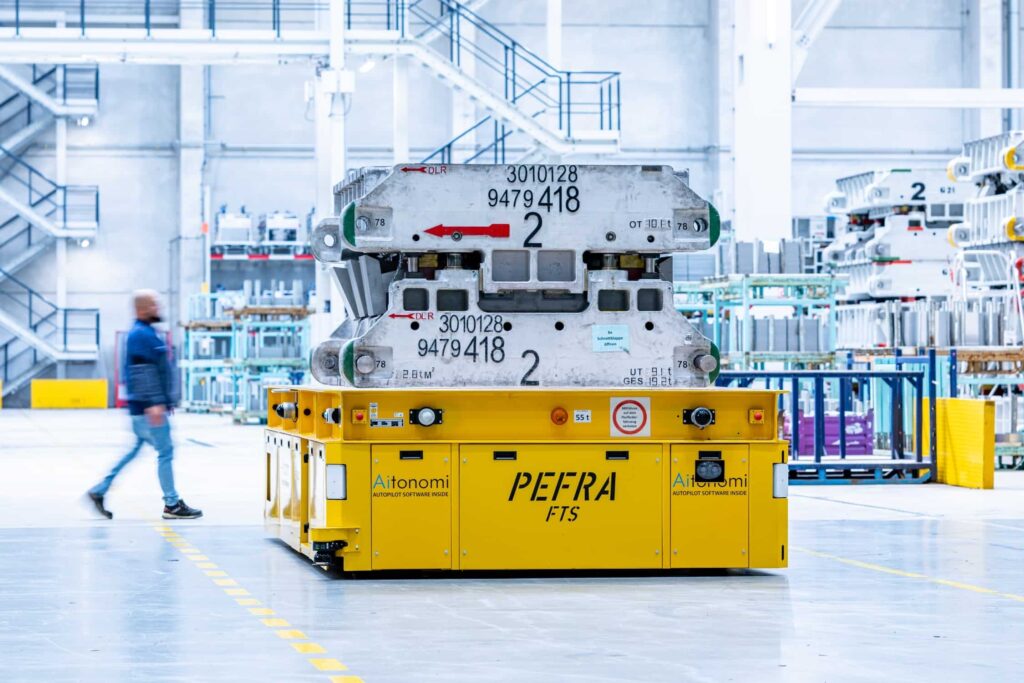
Closed Recycling Loop and Environmental Impact
The Regensburg press shop operates a closed recycling loop, processing around 80,000 tonnes of steel offcuts annually. These offcuts are compacted into 40 x 40 cm steel cubes, each weighing 220 kilograms, which are then sent back to the steel supplier to be made into secondary steel.
This process significantly reduces the plant’s carbon footprint, saving about 160,000 tonnes of CO2 per year, as secondary steel production emits two tonnes less CO2 per tonne compared to primary steel. Additionally, the plant is equipped with sound insulation and minimal vibration systems to protect employees, residents, and the environment from noise and vibrations.
By integrating such advanced technologies and sustainable practices, BMW Group Plant Regensburg exemplifies the future of intelligent, eco-friendly manufacturing.
READ MORE: Polestar 3: An Immersive Sound System Experience
Subscribe today for the freshest car news delivered to your inbox