General Motors is harnessing additive manufacturing, commonly known as 3D printing, to enhance efficiency, lower costs, and improve safety across its operations.
This innovative process creates intricate three-dimensional parts by layering materials from digital designs, a practice GM has refined over 30 years.
From prototyping and production to motorsports, the technology is transforming applications in design, engineering, manufacturing, and aftersales.
READ MORE: Acura Revives RSX Nameplate with Next-Generation EV; Prototype Road Testing Underway
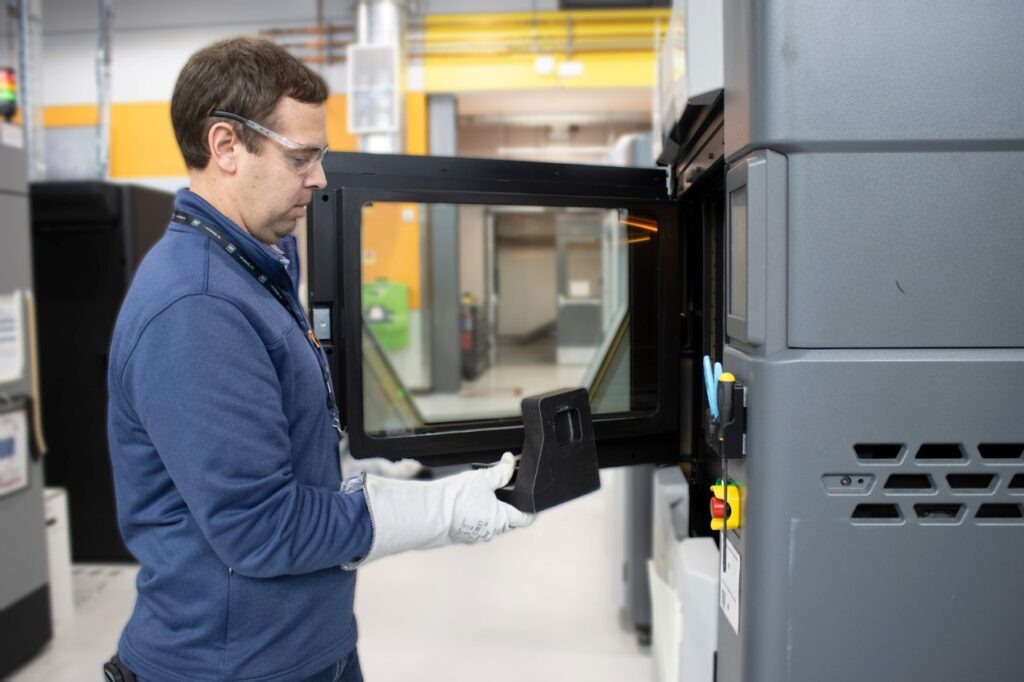
One standout use is in assembly plants, where additive manufacturing streamlines processes and boosts ergonomics. At the Lansing Delta Township Assembly plant, operators previously used a 14-pound metal fixture to prop open vehicle hoods—a weight exceeding the one-hand lift limit of 10 pounds.
The team collaborated with GM’s additive manufacturing experts to create a lightweight 3D-printed alternative, improving safety and usability.
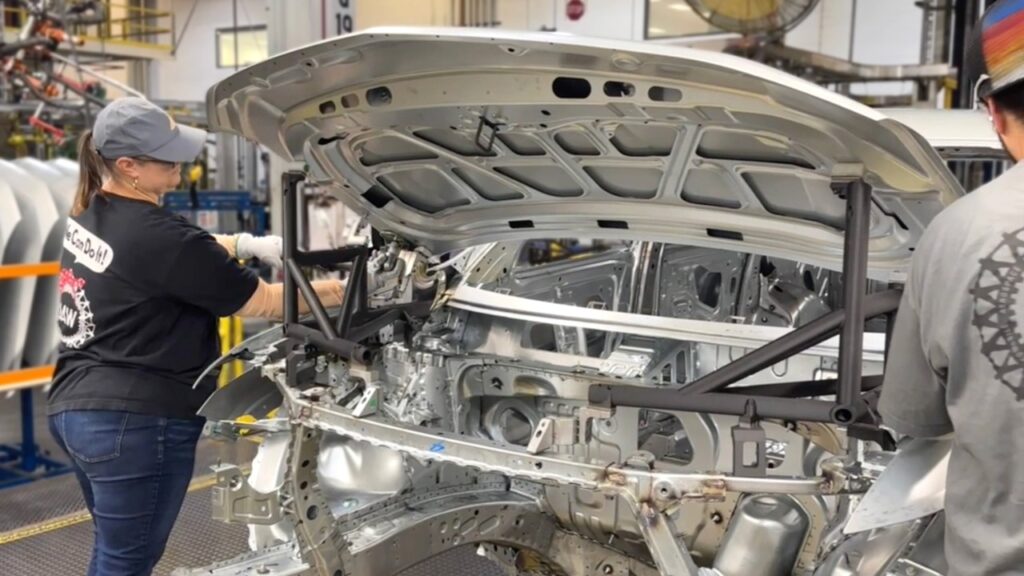
In 2024, GM completed over 5,400 additive manufacturing projects, ranging from accelerated tool development to custom solutions addressing ergonomic challenges.
Paul Wolcott, a GM technical specialist, highlighted the growing role of additive manufacturing in solving practical problems and supporting safer, faster vehicle production.
As GM advances toward an all-electric future, the versatility of additive manufacturing will play a pivotal role in bridging design and production challenges, offering innovative solutions across the board.
READ MORE: Stellantis Reports Q4 2024 Shipments of 1.395 Million Units, a 9% Year-Over-Year Decline
Subscribe today for the freshest car news delivered to your inbox